Like many of you, I’ve been working mostly from home for over 9 months now. And, like many of you, I’ve tried performing my daily work routine from a few different locations in my home. Seeking out the perfect spot for efficiency and for productivity. But also needing to be able to step away from work at the end of the day.
Right now I’m set up in our guest room which may not be the best work location in the house but it definitely lets me step away and forget about work at the end of the workday.
One thing that made our guest room not ideal for working was the desk situation. But I think I’ve fixed the problem.
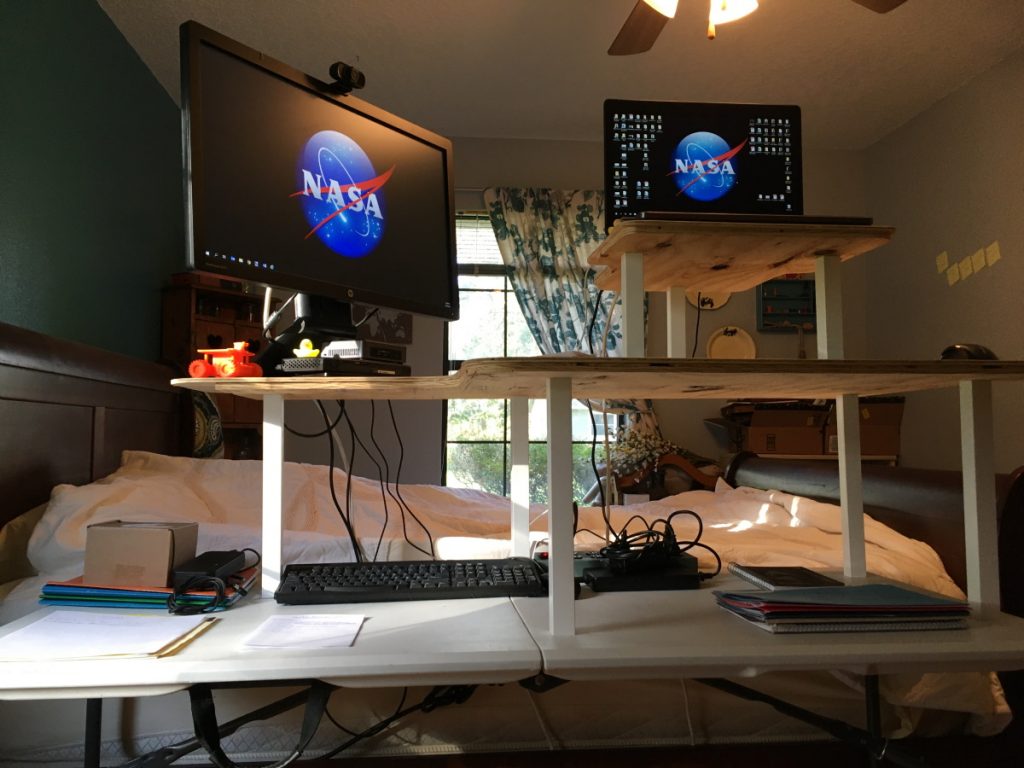
I started with a base desk which is just a 6 foot plastic folding table. But I really wanted a standing desk for good posture and for back strength. One option would be to raise the table itself to the correct height for standing rather than sitting.
Putting the table legs up on blocks of some sort would accomplish that goal fairly easily and inexpensively. But it would also keep me from sitting which I would probably want to do occasionally. So what other options are there other than buying one of those really expensive motorized adjustable standing desks?
It occurred to me that the entire surface didn’t need to be at standing height. Just the part of the tabletop that holds the laptop, keyboard, mouse, and 2nd monitor. So I grabbed some cardboard and I started measuring and cutting out a template.
Here’s what I came up with:
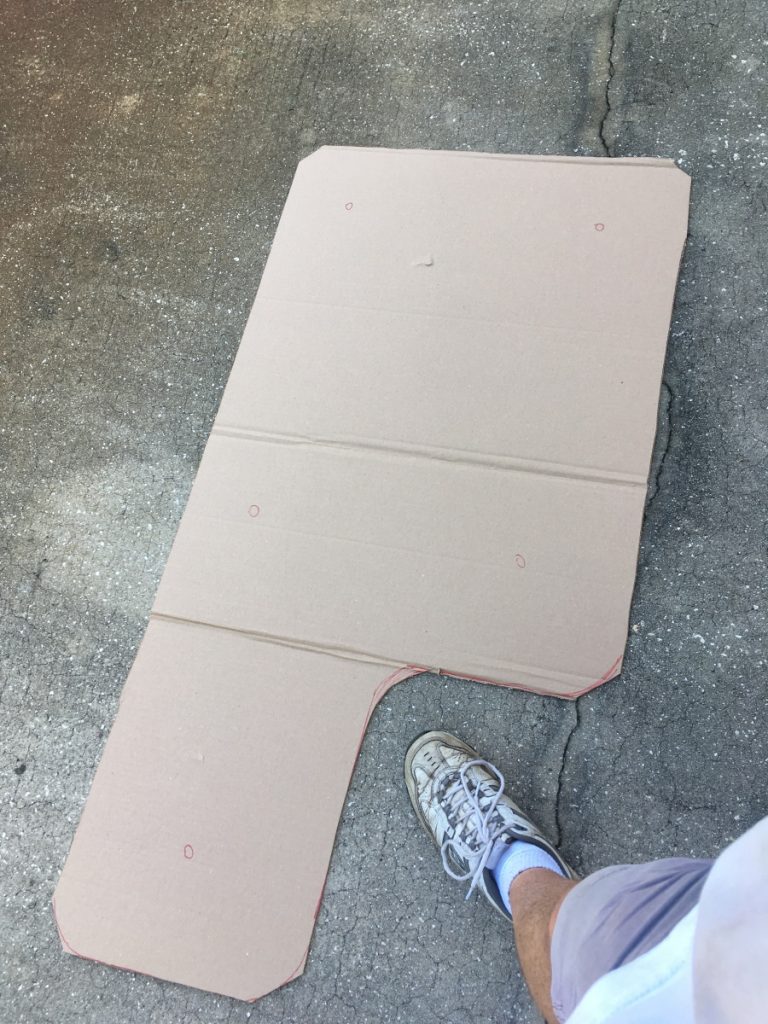
Then I went out to my shop and made this new tabletop out of some scrap wood that’s been out there collecting dust for years.
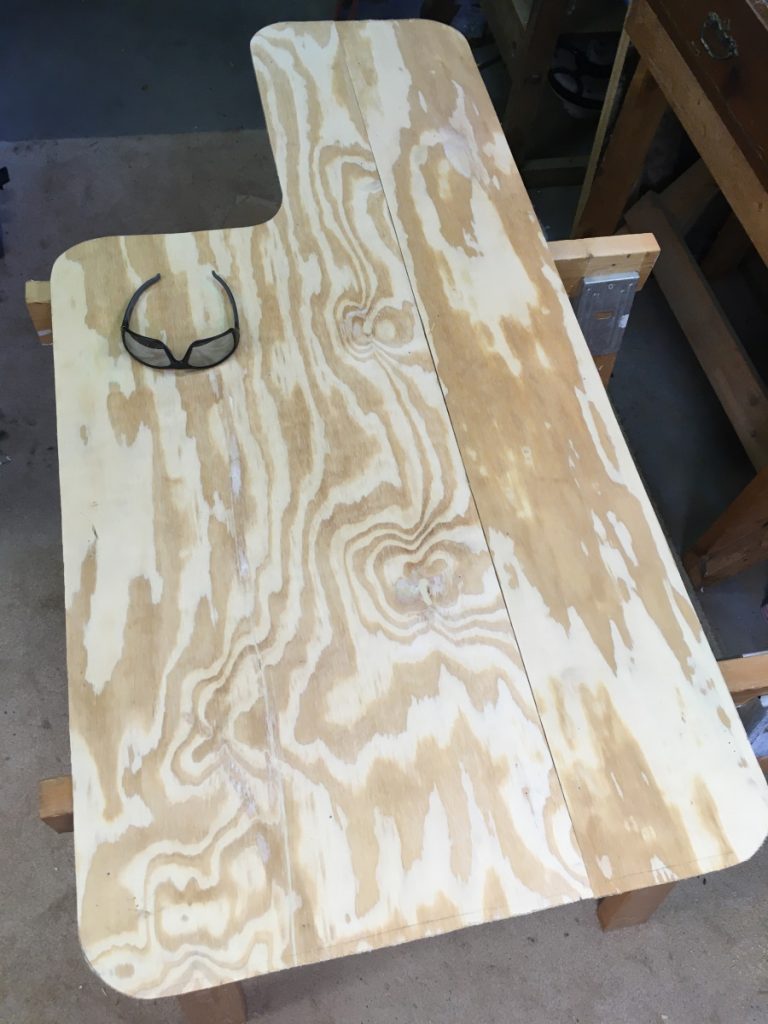
At first I wasn’t sure how to hold up this new tabletop above the base plastic table. So I just temporarily used some old milk crates and some scrap 2x4s to get it to the exact height that would fit my elbows and eyeballs. This temporary configuration allowed me to try it out and make sure the height was correct before committing.
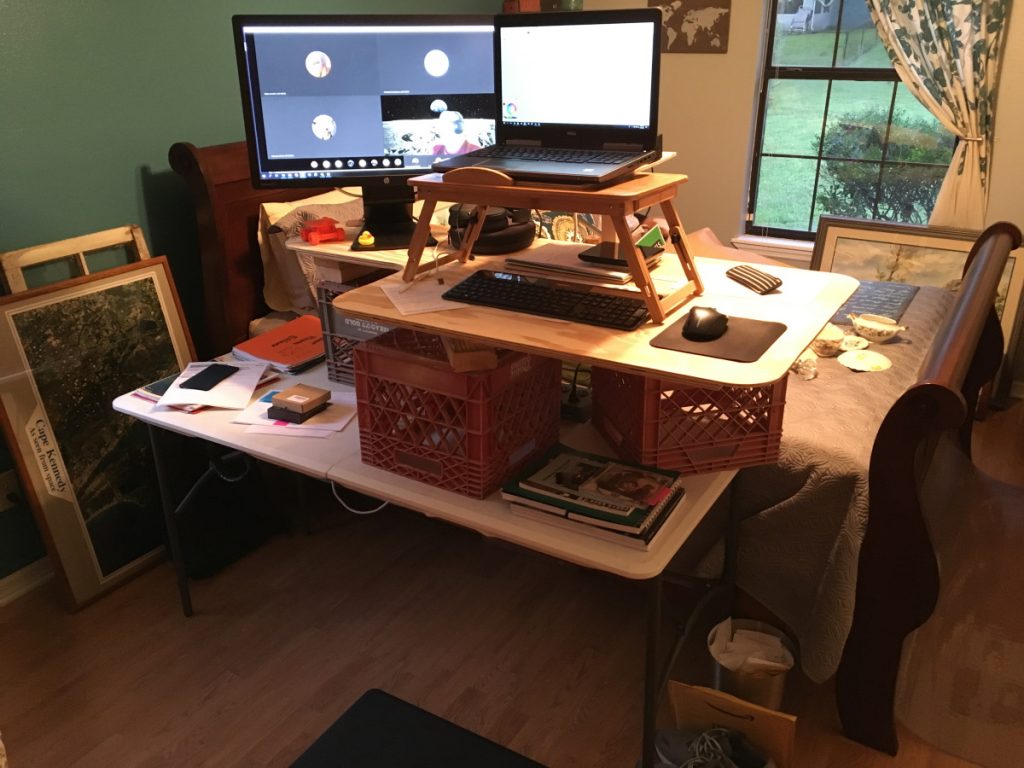
Essentially I had created a desk with different levels for different uses. On the right side is where I stand and do most of my daily work. But the notched area on the left side is where I can sit down at the table and read or write or think or whatever.
After a few months of working in this temporary configuration, I bought some solid inch square stair rail balusters which are the vertical pieces of the stair rail sometimes called spindles. I cut them to the exact length I needed and just screwed them to my custom tabletop.
I also made a smaller tabletop for my laptop and docking station and I used the same balusters as legs, which takes up less room than the little wooden lap desk that I was using before. Just need to paint the plywood surfaces and it will be complete!
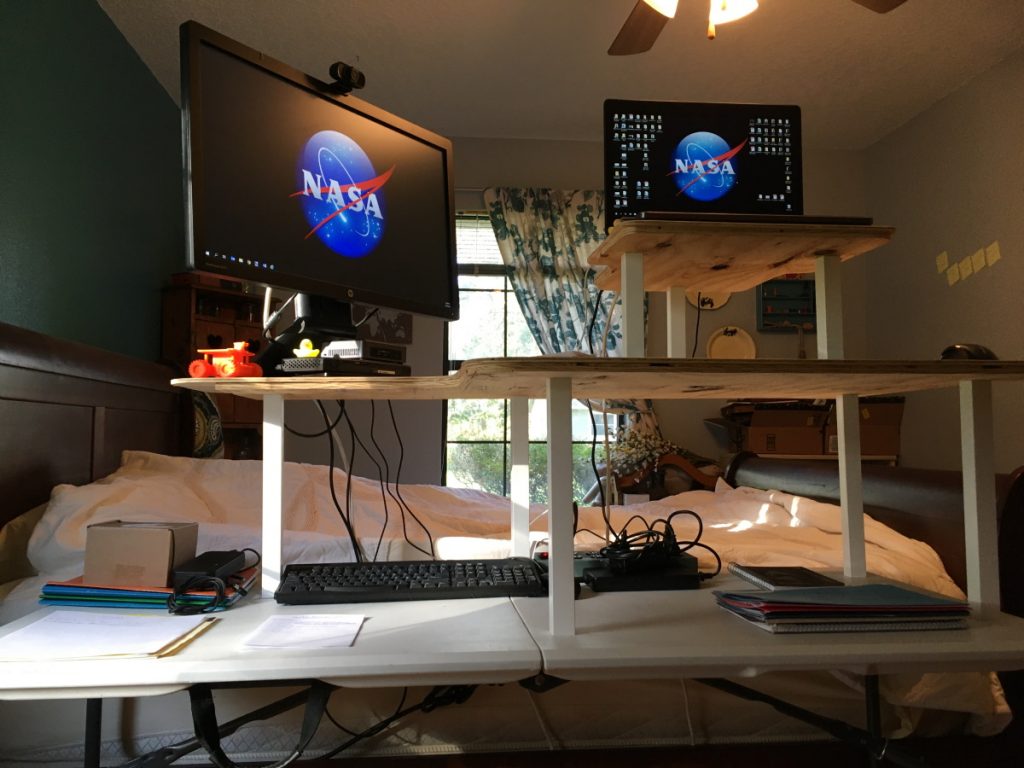
An unplanned by-product of this multi-level desk design is that I ended up with some decent storage space between the levels. There’s actually enough space down there to organize and store folders and papers and books and stuff like that.
I’m really happy with this design and I’m even more happy about how inexpensive it was to build!
If you have any more ideas or suggestions, please leave a comment below!
Thanks for your interest!
Kurt